TR2012-025
High Accuracy NC Milling Simulation Using Composite Adaptively Sampled Distance Fields
-
- "High Accuracy NC Milling Simulation Using Composite Adaptively Sampled Distance Fields", Computer-Aided Design, Vol. 44, No. 6, pp. 522-536, June 2012.BibTeX TR2012-025 PDF
- @article{Sullivan2012jun,
- author = {Sullivan, A. and Erdim, H. and Perry, R.N. and Frisken, S.F.},
- title = {{High Accuracy NC Milling Simulation Using Composite Adaptively Sampled Distance Fields}},
- journal = {Computer-Aided Design},
- year = 2012,
- volume = 44,
- number = 6,
- pages = {522--536},
- month = jun,
- url = {https://www.merl.com/publications/TR2012-025}
- }
,
- "High Accuracy NC Milling Simulation Using Composite Adaptively Sampled Distance Fields", Computer-Aided Design, Vol. 44, No. 6, pp. 522-536, June 2012.
-
Research Area:
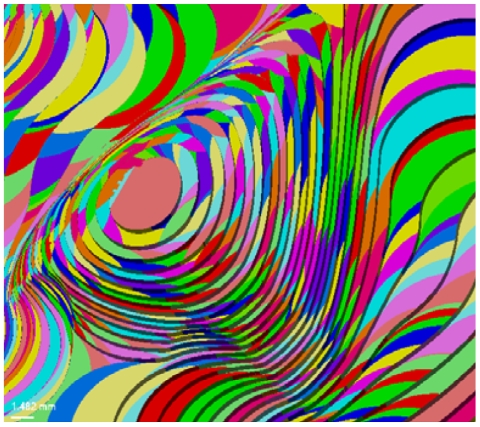
Abstract:
We describe a new approach to shape representation called a composite adaptively sampled distance field (composite ADF) and describe its application to NC milling simulation. In a composite ADF each shape is represented by an analytic or procedural signed Euclidean distance field and the milled workpiece is given as the Boolean difference between distance fields representing the original workpiece volume and distance fields representing the volumes of the milling tool swept along the prescribed milling path. The computation of distance field of the swept volume of a milling tool is handled by an inverted trajectory approach where the problem is solved in tool coordinate frame instead of a world coordinate frame. An octree bounding volume hierarchy is used to sample the distance functions and provides spatial localization of geometric operations thereby dramatically increasing the speed of the system. The new method enables very fast simulation, especially of free-form surfaces, with accuracy better than 1 micron, and low memory requirements. We describe an implementation of 3 and 5-axis milling simulation.
Related News & Events
-
NEWS Computer-Aided Design: publication by Ronald N. Perry, Alan Sullivan and others Date: June 1, 2012
Where: Computer-Aided Design
Research Area: Computer VisionBrief- The article "High Accuracy NC Milling Simulation Using Composite Adaptively Sampled Distance Fields" by Sullivan, A., Erdim, H., Perry, R.N. and Frisken, S.F. was published in Computer-Aided Design.